Los tratamientos térmicos que se pueden aplicar sobre una pieza por impresión 3D FFF en general van a estar dedicados, en su mayoría, a tareas como retirar partes sobrantes de una pieza, como soportes de impresión auxiliares, a intentar corregir la presencia de posibles fallos en la impresión, a mejorar los acabados superficiales o a realizar la unión de las diferentes partes que compondrán una pieza final.
En la mayoría de los casos estas operaciones de reparación y/o mejora consistirán más en pequeños arreglos que devuelvan, si ello es posible, la funcionalidad o la estética a la pieza más que en técnicas estandarizadas. Entre los problemas típicos a solucionar están la presencia de rebabas de filamento, los desprendimientos entre capas de impresión o la rotura de partes de las piezas. Dadas las características de los termoplásticos, si la temperatura alcanzada en el proceso de calentamiento no ha sido excesiva, al enfriarse el material este recuperará de nuevo sus propiedades originales.
En la siguiente descripción de los posibles tratamientos térmicos post-impresión distinguiremos entre los procesos que pueden realizarse por calentamiento directo sobre el material de la pieza y aquellos en los que se realiza un aporte de material fundido extra a la pieza.
Hay que recordar que los procedimientos aquí presentados pueden ser complementados a posteriori con otros tratamientos (mecánicos, químicos, etc.) para mejorar aún más el acabado final de nuestra pieza. Nuevamente los resultados van a variar mucho en función de la maña y experiencia de la persona que los aplica, y cuando se trata de reparaciones, muchas piezas simplemente resultaran irrecuperables.
Calentamiento directo
En el caso de los termoplásticos, como los utilizados en las impresoras 3D FFF, el calentar el material cerca de su punto de fusión (a la llamada temperatura de transición) logra que este se ablande y adquiera cierta plasticidad. Lógicamente, cuando se supera esta temperatura, el material se vuelve líquido, con todas las características que ello implica, como la capilaridad. Esta va a hacer que el material fluido tienda a rellenar los pequeños huecos superficiales existentes en la pieza.
Para calentar el material de la pieza se pueden usar herramientas muy variadas, que van desde equipos profesionales de soldadura por aire caliente (pistolas que incluyen diferentes cabezales en función de la operación a realizar) hasta opciones más asequibles como decapadores para pintura de aire caliente, secadores del pelo, soldadores de estaño, planchas, uso de llamas directas, etc.
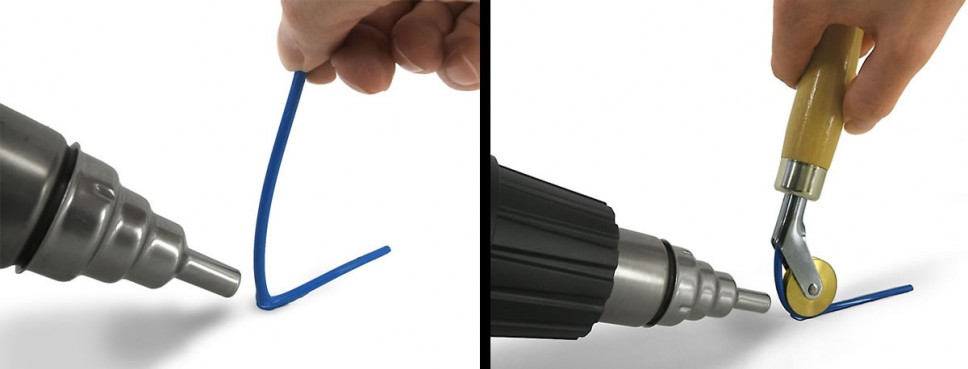
Entre las posibles operaciones que podremos realizar con un estañador tenemos, por ejemplo, el retirar los excesos de material o las rebabas con mayor facilidad que al utilizar, por ejemplo, una simple cuchilla, ya lo que lo haríamos con el material en frío y por tanto mucho más duro.
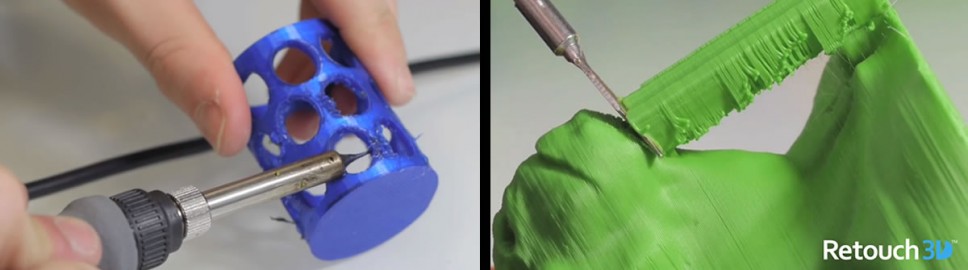
Otra posibilidad, para la se necesita superar el punto de fusión del material, es la de intentar refusionar las capas que tras la impresión han quedado separadas, incluso aquellas partes desprendidas. Para ello se calienta la zona mientras se aplica presión en sentido perpendicular al plano de impresión. Para ello puede utilizarse la punta de un estañador o una pistola de aire caliente.
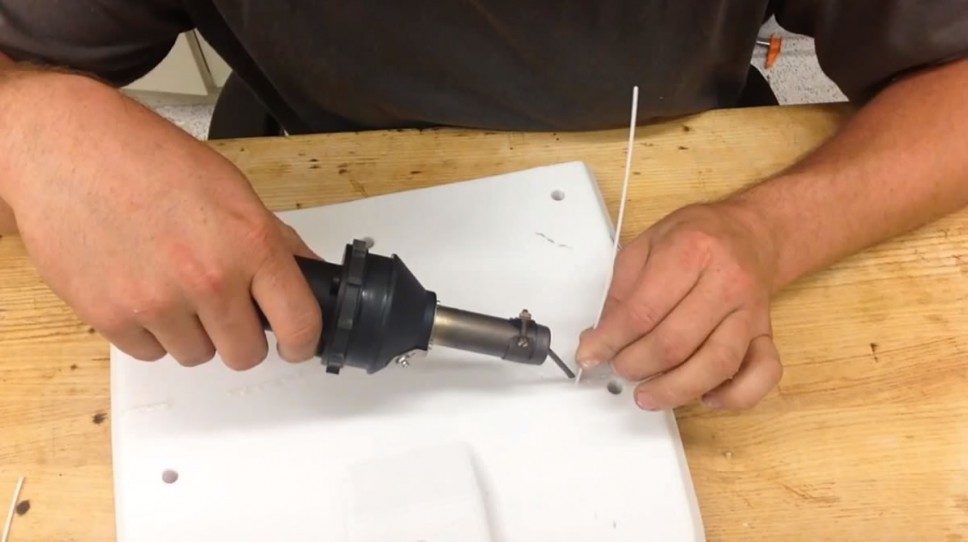
Muy interesante resulta la utilización de pistolas de aire caliente para que las partes de las piezas sometidas a tratamientos mecánicos, como lijados o limados, recuperen su color y brillo original ya que suelen quedar apagadas o mate tras el procedimiento. Una pasada rápida de aire caliente funde una fina capa superficial de la pieza y mejora el acabado.
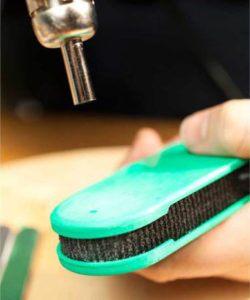
No obstante, el hándicap de aplicar calor directo sobre la pieza reside en que esto va a provocar una plasticidad/fusión en el material que puede afectar en mayor o menor medida a su calidad dimensional. Por ello, cuanto más localizada es la aportación de calor, evitando que este afecte a otras partes de la pieza, mejores son los resultados en general. Por eso estos procedimientos deben ser aplicados con cautela y recurrir prioritariamente, si ello es posible, a cualquiera de los otros tratamientos posibles para solucionar el problema detectado, como los mecánicos, de pegado, etc.
Otras veces, el calentamiento es utilizado precisamente para lograr esa plasticidad en el material. Un caso típico es el de facilitar la introducción de tuercas y otras piezas metálicas en los huecos previstos para ellas en una pieza, en especial, cuando por problemas de exceso de material estas no entran o bien se pretende que queden fijas en la pieza. En la mayoría de los casos, calentar la tuerca o pieza metálica, simplemente apretando contra ella un estañador a la vez que se esta se coloca, facilita el proceso de su montaje al fundir el exceso de material. Al enfriarse el termoplástico, la pieza queda fija.
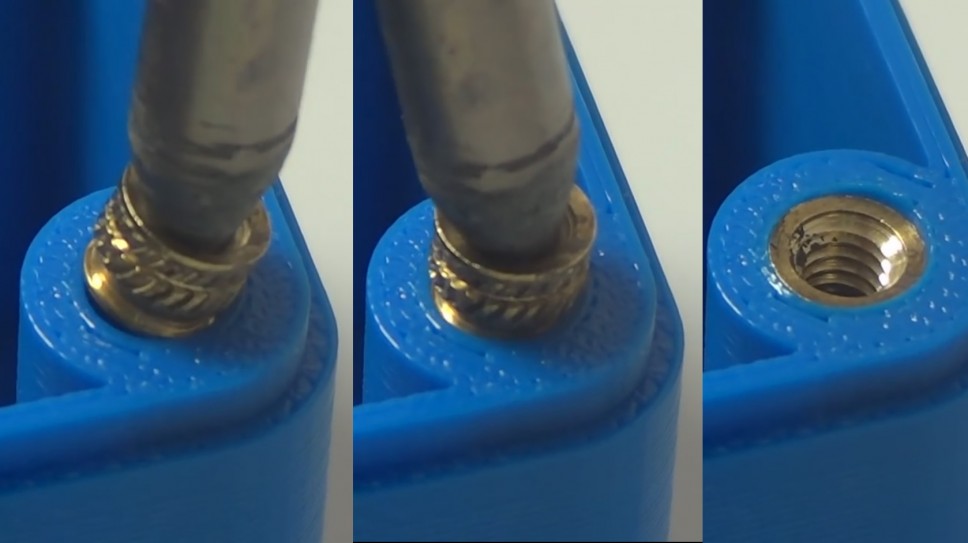
Más “artística” es la posibilidad de utilizar la plasticidad que se logra con el calentamiento para realizar un moldeo manual superficial sobre la pieza, por ejemplo, utilizando diferentes tipos de puntas montadas en un estañador o similar. El objetivo buscando ahora sería aumentar el nivel de detalle y calidad de los acabados. Hablaríamos ya casi de un esculpido manual de la pieza y, de hecho, ya están empezando a aparecer en el mercado herramientas específicamente diseñadas para ello que recuerdan a las utilizadas en el moldeo de la arcilla.
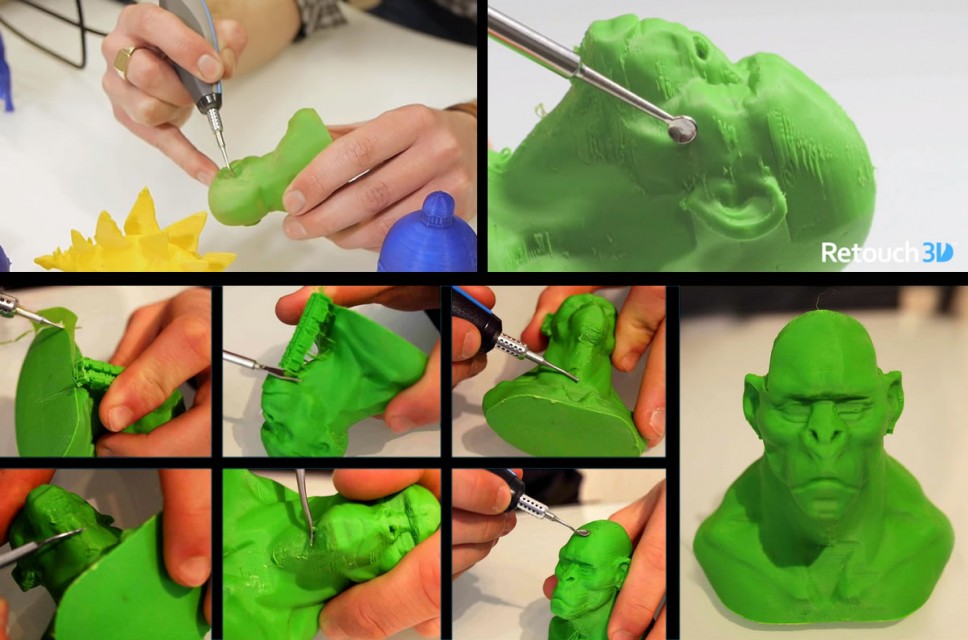
Otra posibilidad que permite la plasticidad que se logra por calentamiento de los termoplásticos es el llamado termoformado de piezas. Este suele utilizarse para obtener ciertas piezas cuya impresión directa resultaría compleja. Por ejemplo, aquellas piezas cuya impresión directa requiria de la utilización de múltiples soportes, pero que pueden obtenerse indirectamente al doblar/deformar de una pieza mucho más fácil de imprimir, por ejemplo, con caras planas. Se imprime esta pieza base, se calienta a la temperatura de transición (por ejemplo, 60ºC para el PLA) y se dobla, por ejemplo, apoyando la cara plana contra un tubo del diámetro adecuado. Al enfriarse la pieza mantendrá la nueva forma adquirida.
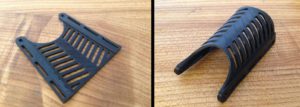
En el caso de otros materiales y técnicas de impresión, los tratamientos térmicos si se corresponden con verdaderos procedimientos estandarizados. Es el caso, por ejemplo, de los llamados ABS digitales (que básicamente son composites a base de diferentes tipos de resinas) utilizados en la tecnología Polyjet, o el caso de las piezas obtenidas con las técnicas basadas en el uso de polvo con aglutinantes. En estas tecnologías de impresión 3D se emplea un paso final consistente en el empleo de hornos específicos para realizar un tratamiento térmico sobre la pieza. Estos permiten a las piezas consolidarse y endurecerse hasta adquirir las propiedades finales buscadas.
Y un caso similar es el de las piezas obtenidas por tecnologías de sinterizado, donde las piezas se introducen en hornos para someterlas a un proceso de recocido (annealing) que active la difusión interna de las partículas de material. Entre otros efectos, esto suele favorecer la disminución de la fragilidad, así como de la porosidad en la pieza, tanto interna como superficial.
Calentamiento indirecto de material
Estos serían los procedimientos en los que no hay un aporte directo de energía térmica al material de la pieza, sino que lo que se utiliza es un aporte de material, el propio termoplástico, directamente fundido. Pueden utilizarse varias técnicas derivadas del campo industrial dedicado a la soldadura de plásticos.
Así tendríamos técnicas como la soldadura por inyección, la soldadura por extrusión, etc. En el fondo, se trata de equipos que aplican el mismo principio de funcionamiento que las propias impresoras 3D FFF, en los que incluso puede utilizarse el mismo filamento con el que se ha impreso la pieza para utilizarlo como material de relleno/pegado al fundirlo. Se trata de equipos relativamente caros y especializados, por lo que su uso queda reservado en la práctica a usuarios avanzados y entornos industriales.
Una técnica, en la que no se aplica calor de modo directo, y que es otra opción muy válida para realizar pequeñas reparaciones y soldaduras a nivel superficial, es la soldadura por fricción (“Friction welding”). Para ello existen herramientas específicas, los llamados soldadores por giro (”spin welders”), en los que el calor se produce por el roce a gran velocidad de un trozo de termoplástico contra la pieza, lo que funde el material termoplástico de ambos y da lugar a la soldadura.
Es fácil implementar uno de estos equipos a nivel amateur empleando las típicas herramientas rotatorias multiusos que se usan para realizar pequeños cortes o taladros. En lugar de la herramienta de corte se coloca ahora un trozo de filamento de termoplástico (en principio el mismo de la pieza) en el cabezal, a modo de broca, y se aplica contra la pieza/s en la zona de unión mientras gira. Los resultados obtenidos son bastante aceptables en general.
Finalmente, otro método curioso, en el que no es tan evidente la generación del calor que funde el termoplástico, es la soldadura por ultrasonidos. Mediante un elemento metálico se transmite una vibración al plástico de dos piezas en contacto que agita sus moléculas hasta fundir el material y provocar la soldadura.